Pressure Transmitter
OVERVIEW OF PRESSURE TRANSMITTERS
The pressure transmitters are used for measuring process pressure, hydrostatic level, and liquid or gas volumetric or mass flow rates in all kinds of process applications. there are five different types of instruments to accommodate the wide variety of applications that exist in industry MVC VALVES staff of experienced application engineers is available to help users select among these choices and specify the instrument that provides the best solution for any pressure measurement application.
KEY APPLICATIONS
- Process Control
- Liquid Level Measurement
- Primary Flow Elements
- Pump & Compressor Control
- Hydrostatic Level Measurement
- Oil & Gas
- Chemical & Petrochemical
- Liquid Storage Tanks
- Food & Beverage
- Pharmaceutical
- Marine & Shipping
Products
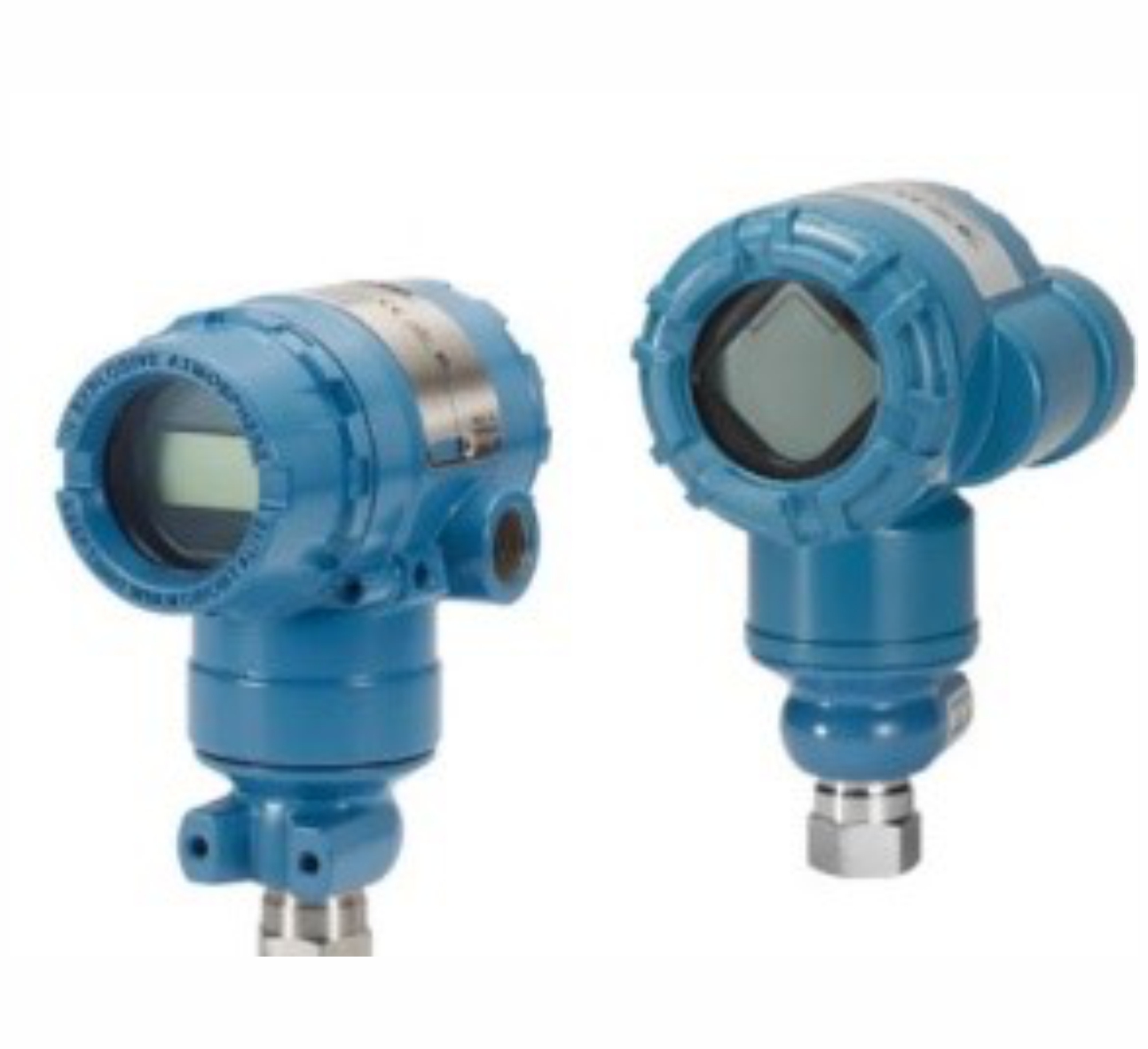

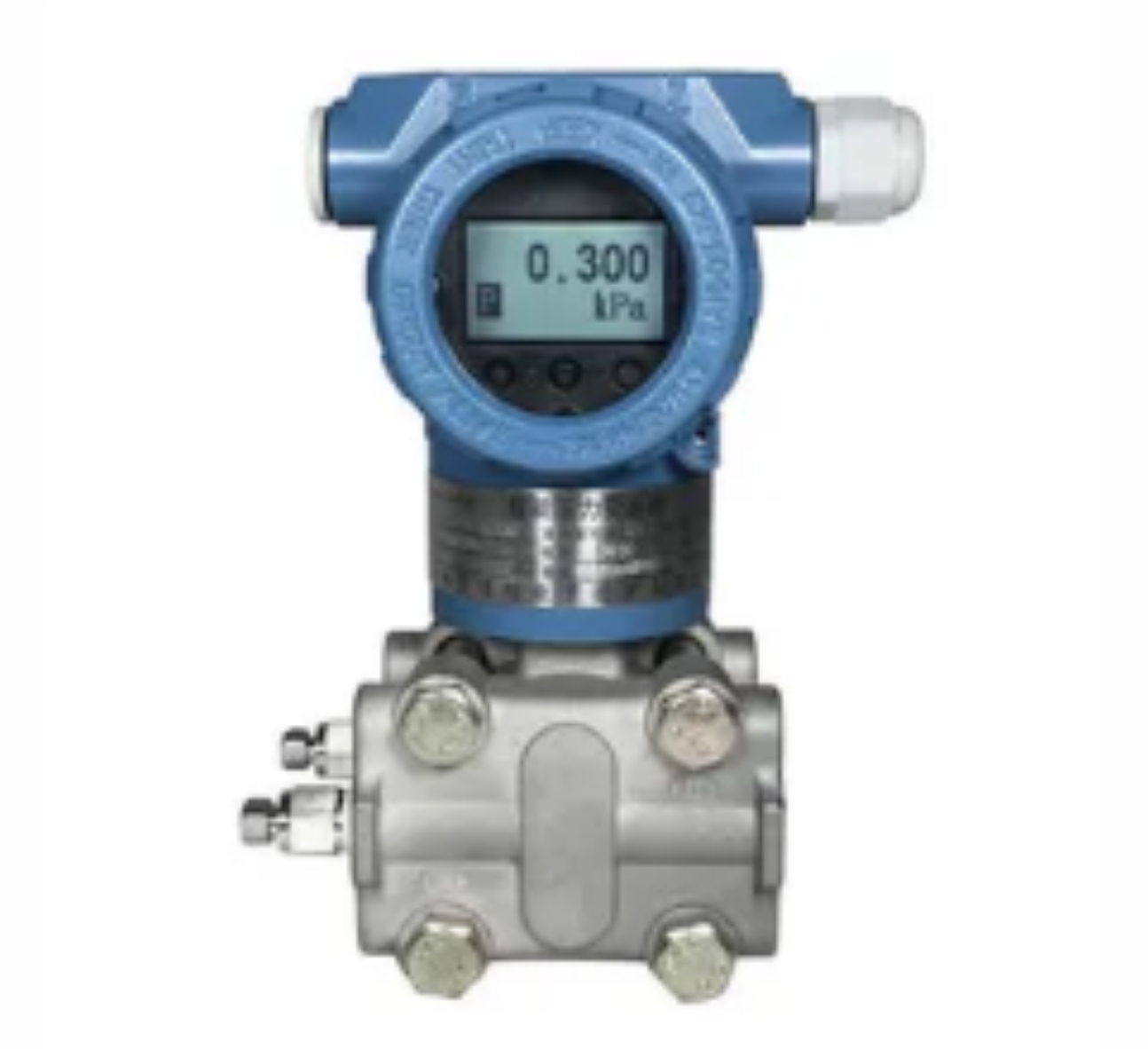
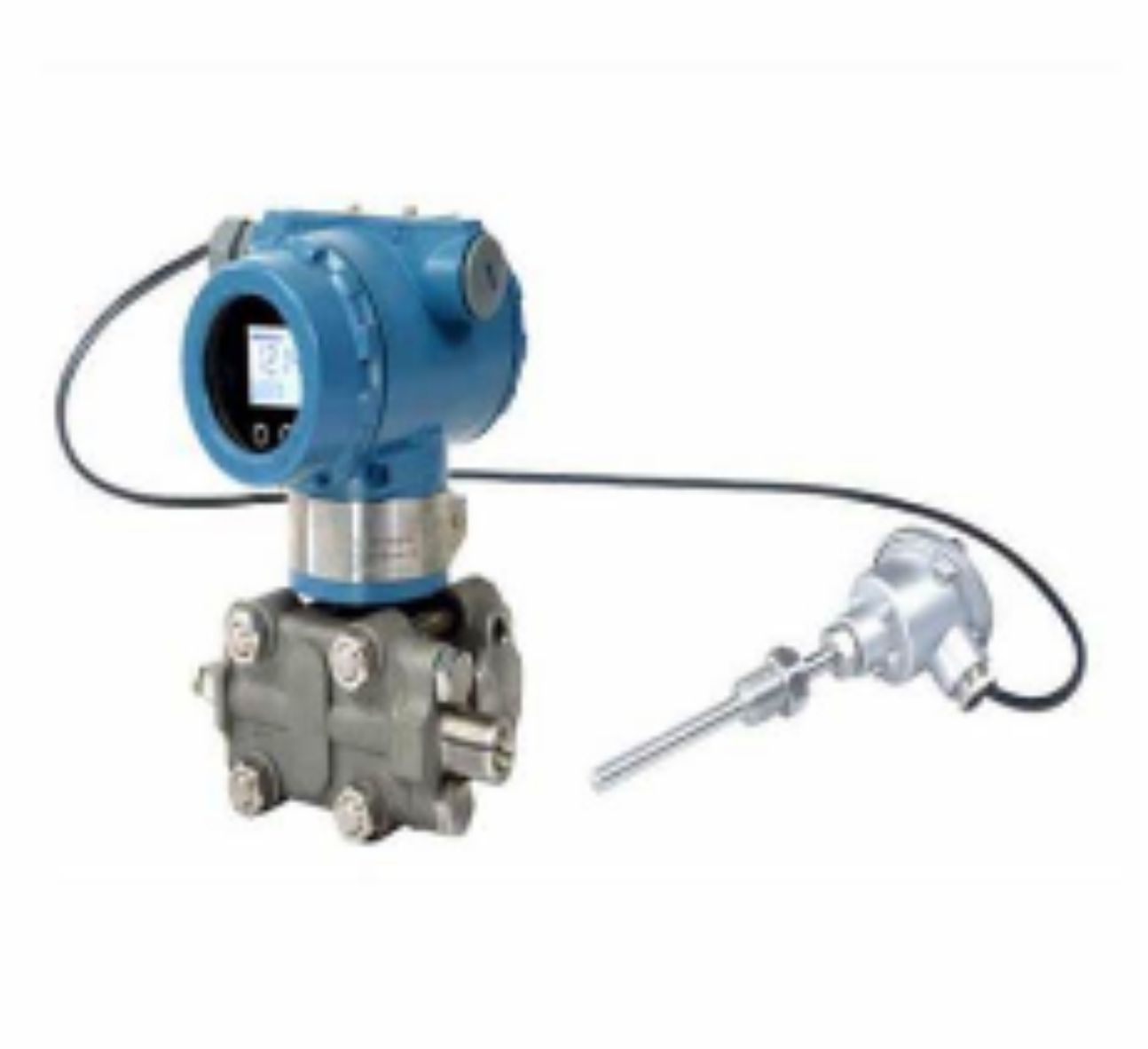
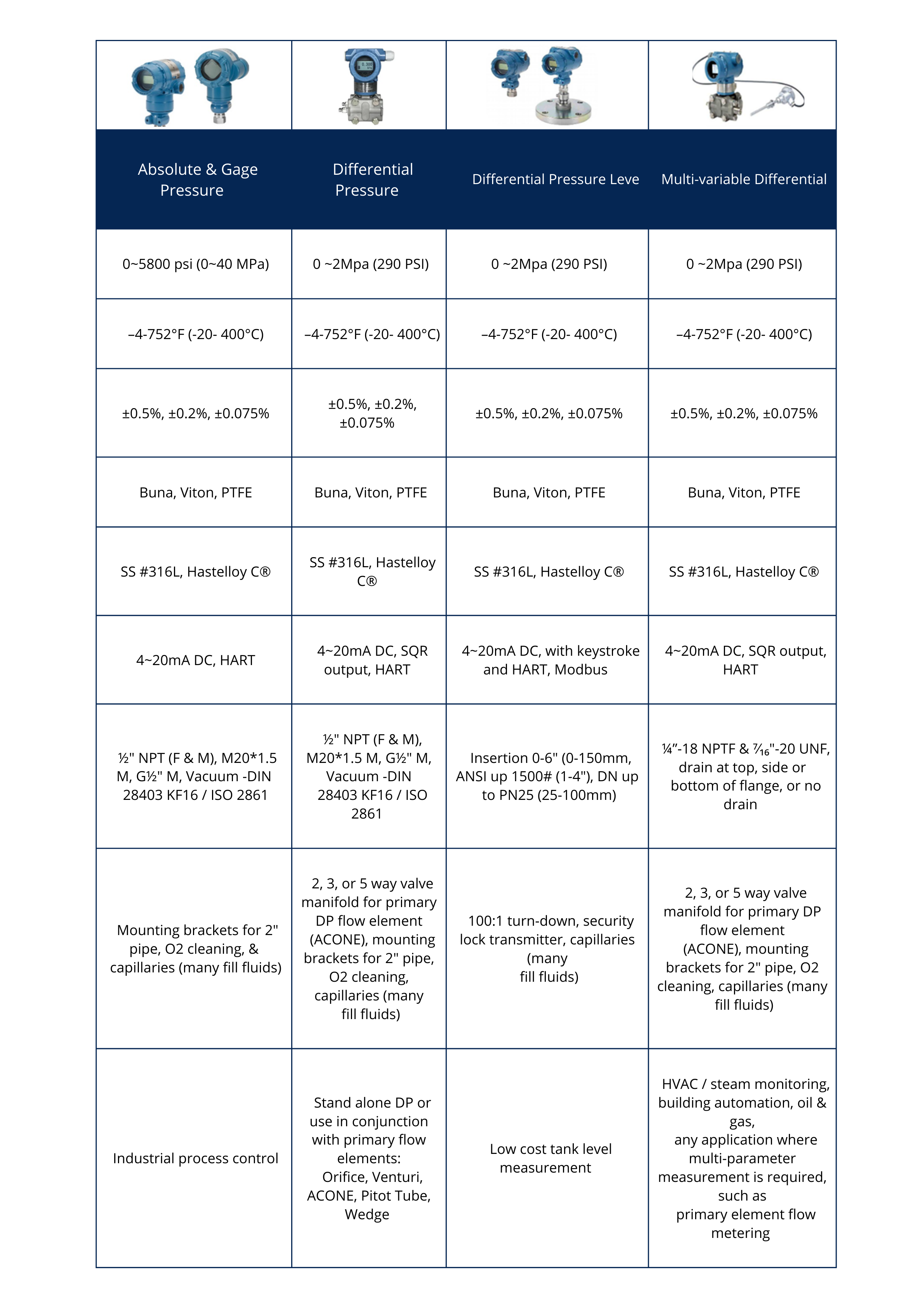
SELECTING A PRESSURE TRANSMITTER
Choosing the ideal pressure transmitter for your application demands careful consideration of various factors. This critical decision can significantly impact process efficiency, safety, and overall system performance. Here’s a comprehensive guide to help you navigate the selection process:
Determine the specific pressure measurement required:
• Absolute pressure transmitters: Measure pressure relative to a perfect vacuum
• Gauge pressure transmitters: Measure pressure relative to atmospheric pressure
• Differential pressure transmitters: Measure the difference between two pressure points.
Select a transmitter that covers your normal operating pressure and potential extremes. Consider the turndown ratio – the ratio between the maximum and minimum measurable pressures. A higher turndown ratio offers greater flexibility but may come at a premium.
Evaluate the required level of accuracy for your application. High-precision pressure transmitters might be essential for custody transfer or critical process control, while standard accuracy may suffice for general monitoring. Remember, accuracy often degrades at the extremes of a transmitter’s range.
Assess the operating environment, including:
• Temperature extremes and fluctuations
• Humidity and potential for condensation
• Exposure to corrosive substances or abrasive materials
• Vibration and shock levels
Choose a transmitter with appropriate materials, seals, and ratings to withstand these conditions without compromising performance.
Determine the required output signal based on your control system’s compatibility:
• Analog: 4-20 mA is common for its noise immunity
• Digital: HART, Fieldbus, or Profibus for advanced diagnostics and multi-variable readings
• Wireless: For hard-to-reach locations or rotating equipment
Consider additional capabilities that might benefit your application:
• Multivariable measurements (e.g., simultaneous pressure and temperature readings)
• Built-in diagnostics for predictive maintenance
• Local displays for easy reading in the field
• Customizable damping to smooth out rapid pressure fluctuations
Look beyond the initial purchase price and consider:
• Installation costs and ease of integration
• Long-term stability and recalibration requirements
• Power consumption, especially for remote or battery-powered installations
• Availability of spare parts and technical support
Ensure the transmitter’s wetted parts are compatible with your process fluid to prevent corrosion or contamination. This is particularly crucial in industries like food and beverage or pharmaceuticals where product purity is paramount.
Consider potential changes in your process or industry regulations:
• Scalability for potential range adjustments
• Firmware upgradability for new features or improved performance
• Compatibility with emerging IIoT (Industrial Internet of Things) platforms
By meticulously evaluating these factors, you can select a pressure transmitter that not only meets your current needs but also provides long-term value and reliability. Whether you’re monitoring compressed air systems, measuring hydrostatic tank levels, or controlling critical processes in chemical manufacturing, the right pressure transmitter will serve as a cornerstone of your instrumentation strategy, ensuring optimal performance, efficiency, and safety in your operations.